In the production of sulfuric acid, one of the essential steps is the melting of sulfur. This process involves heating solid sulfur to its molten state, where it can be further processed into sulfur dioxide and eventually converted into sulfuric acid. The sulfur melting pit is a crucial component of the sulfuric acid plant, where this melting process takes place. Given the high temperatures and highly corrosive nature of sulfur and sulfuric acid, the materials used to construct the sulfur melting pit must be carefully chosen for their thermal resistance and corrosion resistance.
In this article, we will explore the key materials used in constructing sulfur melting pits, the factors that influence material selection, and the significance of these materials in maintaining the integrity and efficiency of a sulfuric acid plant.
Understanding the Sulfur Melting Process in Sulfuric Acid Plants
Sulfuric acid is one of the most important industrial chemicals, used in a variety of applications such as in fertilizers, petroleum refining, and chemical manufacturing. The process of manufacturing sulfuric acid typically involves a few critical steps:
Sulfur Combustion: The first step involves the combustion of sulfur to produce sulfur dioxide (SO₂) gas.
Conversion to Sulfur Trioxide (SO₃): The sulfur dioxide is then oxidized in the contact process to form sulfur trioxide (SO₃).
Sulfuric Acid Formation: The sulfur trioxide is then absorbed in water to form sulfuric acid.
In the initial stages, solid sulfur needs to be melted to facilitate its combustion. The sulfur melting pit is the vessel where solid sulfur (usually in the form of blocks or granules) is heated to a temperature of around 115°C to 120°C (the melting point of sulfur). Once melted, the sulfur is pumped into the combustion chamber for further processing.
Key Characteristics of Sulfur and Its Impact on Material Selection
Sulfur, in its molten state, presents several challenges when it comes to the materials that come in direct contact with it. Here are some of the key characteristics of molten sulfur that affect material selection:
High Temperature: Molten sulfur is typically maintained at temperatures between 115°C and 160°C. This requires materials that can withstand high temperatures without degrading or losing structural integrity.
Corrosive Nature: Molten sulfur and the resulting sulfuric acid are highly corrosive, which can cause rapid deterioration of materials that are not resistant to sulfur or sulfuric acid.
Thermal Shock: The melting process involves significant temperature fluctuations, leading to the risk of thermal shock, where materials may crack or break when exposed to sudden temperature changes.
Given these factors, the materials used in constructing the sulfur melting pit must possess thermal resistance, corrosion resistance, and durability.
Materials Used in Sulfur Melting Pits
The design and material selection of a sulfur melting pit are critical to ensuring the safety and efficiency of the sulfuric acid production process. The materials used in constructing these pits must be able to withstand the harsh conditions posed by the molten sulfur. Below are some of the most commonly used materials:
1. Refractory Materials
One of the most common materials used in sulfur melting pits is refractory materials, which are specifically designed to withstand high temperatures. Refractories are materials that retain their strength and integrity when exposed to extreme heat. The most commonly used refractories for lining sulfur melting pits include:
Fireclay: Fireclay is a type of refractory material that is composed of alumina and silica. It is known for its excellent resistance to high temperatures and thermal shock. Fireclay refractories are often used in sulfur melting pits because they can withstand the temperatures at which sulfur melts, while also offering good thermal insulation properties. This helps maintain the heat within the melting pit and improve the efficiency of the melting process.
Silica Bricks: Silica bricks are made from high-purity silica and are ideal for applications where high heat resistance is required. These bricks can withstand temperatures up to 1,600°C, making them suitable for lining sulfur melting pits. In addition to their thermal resistance, silica bricks also have good resistance to thermal shock, which is important given the fluctuations in temperature during the melting process.
High Alumina Bricks: High alumina bricks are composed primarily of aluminum oxide and can withstand temperatures as high as 1,800°C. These bricks have excellent resistance to corrosive environments, which is particularly important in sulfur melting pits where sulfur and sulfuric acid can be highly corrosive.
2. Castable Refractories
In addition to bricks, castable refractories are sometimes used in sulfur melting pits. These materials are in a liquid form when applied and then harden into a solid lining. Castable refractories offer the advantage of being easier to shape and mold, which makes them ideal for creating custom designs for sulfur melting pits. They are particularly useful in areas that require high resistance to abrasion and chemical attack.
The castable refractories used in sulfur melting pits typically include a mixture of alumina, silica, and other binders to provide both thermal resistance and corrosion resistance. This combination ensures that the materials can withstand the high temperatures and corrosive sulfur environment inside the pit.
3. Stainless Steel
In some cases, stainless steel is used in areas of the sulfur melting pit that do not come into direct contact with molten sulfur but still require resistance to corrosion and heat. Stainless steel has a high degree of resistance to corrosion and oxidation, which is essential in an environment where sulfur or sulfuric acid may come into contact with the material. However, stainless steel is typically used in areas that are not exposed to the extreme temperatures of the molten sulfur but are still subject to corrosion.
4. Acid-Resistant Materials
In addition to the refractories and steel mentioned above, sulfur melting pits may also incorporate acid-resistant materials. These materials are selected for their ability to withstand the highly corrosive nature of sulfuric acid, which can form in the melting pit as a byproduct of the sulfur melting process. Acid-resistant bricks and coatings made from materials such as graphite or specialty ceramics are sometimes used to protect the structural components of the pit from corrosion.
Factors Influencing Material Selection
The selection of materials for the construction of a sulfur melting pit is influenced by several key factors. These factors ensure that the pit remains durable and efficient throughout the production process:
1. Temperature Resistance
The material must be able to withstand the high temperatures associated with melting sulfur (around 115°C to 160°C) without degrading. Materials like refractory bricks, silica, and high alumina are specifically designed for these high-temperature environments and prevent thermal damage.
2. Corrosion Resistance
Molten sulfur is corrosive, and the materials used in the melting pit must be able to resist corrosion from both sulfur and sulfuric acid. Refractories like fireclay, silica, and high alumina bricks, along with acid-resistant coatings, offer the required protection against corrosion.
3. Thermal Shock Resistance
Due to the fluctuating temperatures during the melting process, materials must be resistant to thermal shock, which can cause cracking or failure of the material. Silica bricks and high alumina refractories are particularly effective in withstanding thermal shock.
4. Durability and Maintenance
The materials selected must be durable enough to handle prolonged exposure to sulfur, heat, and abrasive wear. Additionally, they must require minimal maintenance to ensure the long-term efficiency of the sulfur melting pit. Refractory linings made from fireclay, silica, and high alumina bricks typically provide the required durability.
Conclusion
The construction of a sulfur melting pit in a sulfuric acid plant requires the use of highly specialized materials that can withstand the extreme conditions created by molten sulfur. Refractory materials, such as fireclay, silica bricks, and high alumina bricks, are commonly used to line the pit, providing excellent heat resistance and corrosion protection. Additionally, castable refractories and acid-resistant materials help ensure the longevity of the pit and its ability to resist damage from sulfur and sulfuric acid.
The careful selection of materials for the sulfur melting pit is critical to the efficiency and safety of sulfuric acid production. By using the right combination of heat-resistant and corrosion-resistant materials, sulfur melting pits can operate efficiently for extended periods, providing a stable foundation for the production of high-quality sulfuric acid.
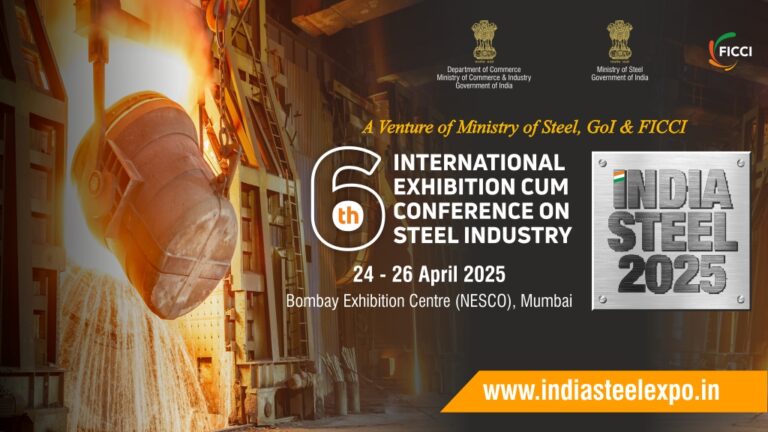