Introduction
Hollow refractory bricks are a critical component in various industrial applications that require the ability to withstand high temperatures. These bricks are designed to provide excellent thermal insulation while maintaining durability in extreme conditions, such as in kilns, furnaces, and reactors. Their lightweight nature, combined with superior insulating properties, makes them ideal for use in industries such as steel manufacturing, cement production, glass manufacturing, and power plants.
In this article, we will explore the process of making hollow refractory bricks, their unique advantages, and the many applications in which they are used. By understanding the manufacturing techniques, materials, and benefits of these specialized bricks, industries can make more informed decisions about their use in high-temperature environments.
What Are Hollow Refractory Bricks?
Hollow refractory bricks are a type of refractory material that is characterized by the presence of air pockets or voids within the brick. These cavities reduce the density of the brick while still allowing it to maintain the high-temperature resistance and strength required for use in industrial settings. The air pockets within the brick provide superior thermal insulation, helping to retain heat and reduce energy consumption in high-temperature applications.
Refractory bricks, in general, are designed to withstand extreme temperatures without breaking down or melting. They are made from materials that possess high melting points and are often used to line furnaces, kilns, incinerators, and other high-heat environments. Hollow refractory bricks serve a similar function but with the added benefit of lower weight and superior insulating properties.
Materials Used in Hollow Refractory Bricks
The raw materials used in the manufacturing of hollow refractory bricks must have high melting points and the ability to withstand thermal shock. Some of the most commonly used materials in the production of these bricks include:
Clay: Fireclay, which is a type of high-alumina clay, is commonly used in the production of refractory bricks due to its ability to withstand high temperatures. Fireclay is often used in applications where moderate heat resistance is needed.
Silica: Silica is another important material in the production of refractory bricks. It has a high melting point, making it suitable for use in extremely high-temperature environments.
Magnesia: This material is used for its excellent resistance to high temperatures and basic slags, making it suitable for applications such as steel manufacturing and other high-temperature industrial processes.
Chromite: Chromite-based refractory bricks are used in environments that require resistance to both high temperatures and chemical corrosion.
Zirconia: Used in specialized applications, zirconia offers extremely high melting points and excellent thermal stability.
The choice of material depends on the specific requirements of the application, including the operating temperature, exposure to chemicals, and thermal shock resistance.
Manufacturing Process of Hollow Refractory Bricks
The manufacturing process of hollow refractory bricks involves several key steps, from raw material selection to the final firing process. The creation of air pockets within the brick is a critical part of the process, as it directly impacts the brick’s thermal insulation properties.
1. Selection of Raw Materials
The first step in making hollow refractory bricks is the selection of appropriate raw materials. As mentioned earlier, materials with high melting points and good thermal resistance properties are chosen. The materials are carefully selected to ensure that the final product will have the desired characteristics for specific applications.
Once the materials are chosen, they are thoroughly mixed to create a uniform blend. This mixture will form the base for the brick.
2. Formation of the Hollow Structure
The hallmark of hollow refractory bricks is their reduced density, which is achieved by incorporating air pockets into the brick. This is typically done through the addition of a foaming agent. A foaming agent is a substance that produces gas or bubbles when mixed with the other raw materials. These gas bubbles create small voids within the material, forming the hollow structure.
The foaming agent can be a chemical compound or organic material that generates gas when heated. The gas forms bubbles within the mixture, creating a porous structure that significantly reduces the density of the final brick while still maintaining its refractory properties. The size and distribution of these air pockets are crucial for determining the insulating capabilities and mechanical strength of the brick.
There are different ways to introduce these air pockets into the material:
Chemical Foaming: This involves the addition of chemicals that release gas when mixed with the other raw materials. These gases form bubbles during the mixing process.
Physical Foaming: In some cases, physical foaming agents, such as expanded polystyrene or other organic compounds, may be added to create the air pockets.
Blended Aggregates: Sometimes, certain aggregates with a naturally porous structure are blended into the mix to create voids.
3. Molding the Bricks
Once the raw material mixture has been prepared and foaming agents have been added, the material is placed into molds. The molding process shapes the mixture into the desired form, whether it be rectangular, square, or custom shapes for specific applications. The molding process ensures that the brick is uniform in shape and size.
At this stage, the foaming agent has created the initial voids, but the air pockets are not fully formed until the brick undergoes the next steps of drying and firing.
4. Drying the Bricks
After the molding process, the bricks are dried to remove any moisture content. This step is essential because excessive moisture can interfere with the firing process and lead to defects in the final product. The bricks are placed in a controlled environment where the moisture content is gradually reduced.
The drying process also helps in stabilizing the shape of the bricks, ensuring that the air pockets are evenly distributed throughout the brick.
5. Firing the Bricks
Firing is the critical stage in the production of hollow refractory bricks. The dried bricks are placed in a kiln and subjected to high temperatures. Firing causes the material to harden, strengthen, and develop the desired refractory properties. The heat also ensures that the air pockets within the brick remain stable and do not collapse.
The firing temperature can vary depending on the materials used, but it typically ranges from 1200°C to 1700°C. During this stage, the foaming agents release gas, creating more air pockets within the brick. The result is a lightweight, durable brick that retains excellent insulation properties.
After firing, the bricks are allowed to cool gradually. The cooling process must be carefully controlled to prevent thermal shock and ensure that the bricks retain their structural integrity.
6. Final Inspection and Adjustments
Once the bricks have cooled, they undergo inspection and quality control checks to ensure they meet the necessary standards for thermal resistance, mechanical strength, and uniformity. Any bricks that do not meet the required specifications are discarded or reprocessed.
In some cases, the bricks may be further treated to enhance their durability or resistance to specific chemicals. For instance, they may be coated with a layer of material to protect them from corrosive environments.
Advantages of Hollow Refractory Bricks
Hollow refractory bricks offer several distinct advantages, making them a popular choice in a variety of industrial applications.
1. Lightweight
The primary benefit of hollow refractory bricks is their lightweight nature. The presence of air pockets reduces the overall density of the brick, making it easier to handle and install. This can be especially important in large-scale construction projects, where the weight of materials can become a significant factor.
2. Thermal Insulation
The air pockets within hollow refractory bricks provide superior thermal insulation properties. The ability of these bricks to retain heat helps to reduce energy consumption and maintain more stable temperatures in high-temperature environments. This insulation capability is especially important in industries such as steel manufacturing and cement production, where maintaining high temperatures is critical for efficiency.
3. Energy Efficiency
Due to their insulating properties, hollow refractory bricks help improve energy efficiency by reducing heat loss in furnaces, kilns, and other high-temperature equipment. This not only reduces operational costs but also helps to conserve energy, making the processes more environmentally friendly.
4. Durability and Strength
Despite being lightweight, hollow refractory bricks are still durable and able to withstand extreme conditions. They maintain their integrity under high heat and mechanical stress, making them reliable in demanding industrial settings.
5. Cost-Effectiveness
Hollow refractory bricks are cost-effective due to their reduced weight and improved insulation properties. They can help lower energy costs, and their lighter weight can also reduce transportation and labor costs, making them a more economical choice for large-scale applications.
Applications of Hollow Refractory Bricks
Hollow refractory bricks are widely used in industries that deal with high-temperature processes. Some common applications include:
Steel Manufacturing: In blast furnaces, steel converters, and other equipment used in the production of steel, hollow refractory bricks provide the necessary insulation to conserve heat and improve energy efficiency.
Cement Production: In cement kilns, where temperatures often exceed 1400°C, hollow refractory bricks help maintain high temperatures and reduce energy consumption.
Glass Manufacturing: The production of glass requires high-temperature furnaces that can benefit from the thermal insulation provided by hollow refractory bricks.
Power Plants: In boilers and reactors, where maintaining high temperatures is crucial, hollow refractory bricks help to improve thermal efficiency and reduce operational costs.
Chemical Industry: Hollow refractory bricks are used to line reactors, furnaces, and other equipment in the chemical industry, where high temperatures are necessary for various chemical processes.
Conclusion
Hollow refractory bricks are an essential material in industries that require high-temperature resistance and excellent thermal insulation. Through a careful manufacturing process that incorporates foaming agents and precise molding, these bricks offer a lightweight, durable, and energy-efficient solution to various industrial needs. Their ability to maintain high temperatures while reducing heat loss makes them indispensable in applications ranging from steel manufacturing to power generation.
By understanding the manufacturing process, benefits, and applications of hollow refractory bricks, industries can make informed decisions on their use, ensuring the longevity and efficiency of their high-temperature systems. With ongoing advancements in materials science, the future of hollow refractory bricks looks promising, continuing to support industries in maintaining energy-efficient, high-performance systems.
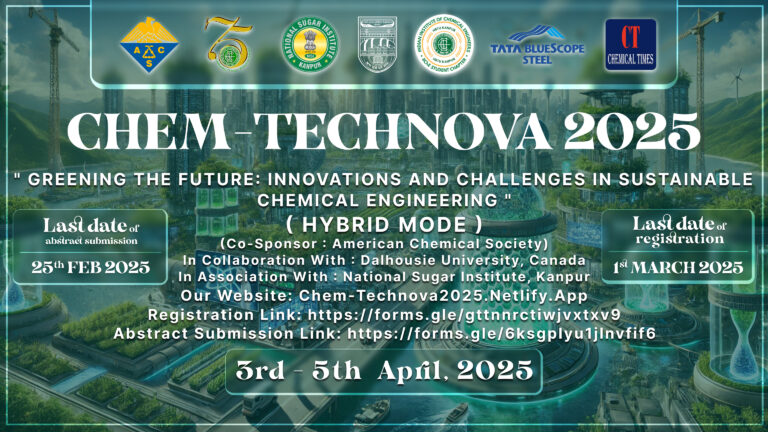