Fireclay bricks, renowned for their durability, heat resistance, and affordability, are widely used in various industrial and residential applications. These versatile materials are an essential component in structures that must endure high temperatures, such as furnaces, kilns, fireplaces, and pizza ovens. However, despite their many advantages, fireclay bricks do have limitations. Understanding these constraints is crucial for selecting the right refractory material for specific applications, as using fireclay bricks in unsuitable conditions can lead to operational inefficiencies or even failures. In this article, we will explore the various situations where fireclay bricks are not ideal, focusing on their temperature limitations, chemical resistance, and other specific characteristics that make them unsuitable for certain uses.
What Are Fireclay Bricks?
Fireclay bricks, a type of refractory brick, are made from fireclay, which is a naturally occurring material composed of alumina (Al2O3) and silica (SiO2). These bricks are widely used in industries that involve heat-intensive processes due to their excellent thermal properties. Fireclay bricks are known for their ability to withstand high temperatures and their relatively low thermal conductivity. This makes them perfect for insulating and lining furnaces, kilns, fireplaces, and chimneys.
The typical temperature range that fireclay bricks can withstand is around 1,400°C to 1,600°C (2,550°F to 2,912°F). This makes them suitable for many applications in which temperatures do not exceed these limits. However, as we will discuss in detail, fireclay bricks are not always the best choice when higher temperatures or more specific environmental conditions are involved.
Fireclay Bricks in High-Temperature Furnaces
One of the primary applications of fireclay bricks is in furnaces. These devices are designed to reach and maintain high temperatures for processes like metal smelting, glass production, or chemical processing. Fireclay bricks perform well in these environments as long as the operating temperature does not exceed their maximum thermal tolerance. However, they are not ideal for use in high-temperature furnaces where temperatures exceed 1,600°C (2,912°F).
For instance, in furnaces used for melting metals like steel or in glass furnaces, the temperatures can often surpass 1,800°C (3,272°F). In these cases, fireclay bricks may degrade due to thermal shock or loss of structural integrity. When exposed to extreme heat beyond their capacity, fireclay bricks may begin to crack, erode, or melt, which can compromise the furnace’s functionality and safety.
To address these higher temperature requirements, specialized refractory bricks made from materials such as alumina (aluminum oxide) or silica are preferred. Alumina bricks, for example, have higher melting points and better resistance to extreme temperatures, making them better suited for high-temperature environments.
In conclusion, while fireclay bricks are excellent for moderate-temperature applications, high-temperature furnaces demand materials that can endure the intense heat without failing. In such cases, alumina or silica bricks are often the better option.
The Use of Fireclay Bricks in Industrial Kilns
Industrial kilns, which are used in the manufacturing of ceramics, bricks, cement, and other products, often operate at high temperatures. Fireclay bricks have traditionally been used to line these kilns because of their ability to withstand the heat generated during the firing process. However, as with furnaces, fireclay bricks have limitations in industrial kilns where temperatures can exceed their maximum heat tolerance.
In industries like cement production, kilns can reach temperatures in excess of 1,800°C (3,272°F), especially in processes like clinker production. Under such extreme conditions, fireclay bricks may begin to degrade due to thermal shock, which occurs when the material expands and contracts rapidly. This can lead to cracks or structural failure.
To avoid these issues, high-alumina refractory bricks are often preferred for such high-temperature kilns. These bricks can tolerate higher temperatures, reducing the risk of failure and extending the life of the kiln. Additionally, other refractory materials like magnesia bricks or zirconia bricks may be used depending on the specific needs of the kiln, especially if the process involves exposure to high heat over extended periods.
In summary, while fireclay bricks are suitable for kilns with moderate temperature requirements, their performance in high-temperature industrial kilns may be compromised. For kilns that operate at extremely high temperatures, alternative refractory materials with higher melting points should be considered.
Fireclay Bricks in Extreme Chemical Environments
Another key factor to consider when using fireclay bricks is their chemical resistance. Fireclay bricks are generally stable in neutral or mildly acidic environments, but they are not ideal for environments where they are exposed to strong acids or bases. The interaction between the chemicals in the environment and the fireclay brick can lead to chemical erosion, weakening the brick over time.
For example, fireclay bricks are not well-suited for use in environments like acidic furnaces or chemical reactors that involve corrosive substances. The acidic conditions can break down the fireclay brick, causing it to lose its integrity and fail. In these situations, more chemically resistant refractory materials such as silica bricks, magnesia bricks, or chromite bricks are preferred due to their superior resistance to chemical attack.
In environments where chemical reactions are a significant factor, it is essential to choose materials that are not only thermally stable but also resistant to corrosion. Alumina-based refractories are often used in such conditions, as they exhibit strong resistance to acids, alkalis, and other reactive chemicals.
Thus, while fireclay bricks perform well in many general applications, they are unsuitable for areas exposed to high chemical stress or corrosive environments. For such applications, materials with higher chemical resistance should be selected to ensure long-lasting performance and safety.
Fireclay Bricks and Their Performance Under Thermal Shock
Thermal shock refers to the damage that occurs when a material is subjected to rapid temperature fluctuations, causing it to expand and contract quickly. Fireclay bricks, while excellent at withstanding consistent high temperatures, are more susceptible to damage from thermal shock than some other refractory materials. This is because the alumina and silica content in fireclay bricks can cause them to expand unevenly when exposed to sudden temperature changes.
This makes fireclay bricks less ideal for applications where the temperature fluctuates dramatically. In industrial settings like blast furnaces or foundries, where temperatures can change rapidly due to the introduction of cold materials or the sudden opening of furnace doors, thermal shock can cause the fireclay bricks to crack or break apart. In such conditions, refractories that are specifically designed to resist thermal shock, such as zirconia-based or silicon carbide bricks, are often a better choice.
Conclusion
Fireclay bricks are an essential material in various industries due to their excellent heat resistance and affordability. However, they do have limitations that need to be considered in order to select the best refractory material for each specific application. Fireclay bricks are not suitable for environments that exceed their maximum temperature resistance, such as high-temperature furnaces or industrial kilns. They also have limited chemical resistance, making them unsuitable for highly corrosive environments. Additionally, fireclay bricks are vulnerable to thermal shock, which can compromise their performance in situations where temperatures fluctuate rapidly.
To ensure optimal performance and safety, it is crucial to evaluate the specific needs of an application and select the appropriate refractory material accordingly. While fireclay bricks are ideal for moderate-temperature applications like fireplaces, pizza ovens, and general furnace linings, higher-temperature or more chemically aggressive environments require the use of specialized refractory materials such as alumina, silica, magnesia, or zirconia bricks.
By understanding the limitations of fireclay bricks and selecting the appropriate materials for high-temperature or chemically demanding applications, industries can improve operational efficiency and extend the lifespan of their equipment. Therefore, while fireclay bricks remain a reliable and cost-effective choice for many applications, recognizing when they are not suitable is key to ensuring long-term success in industrial operations.
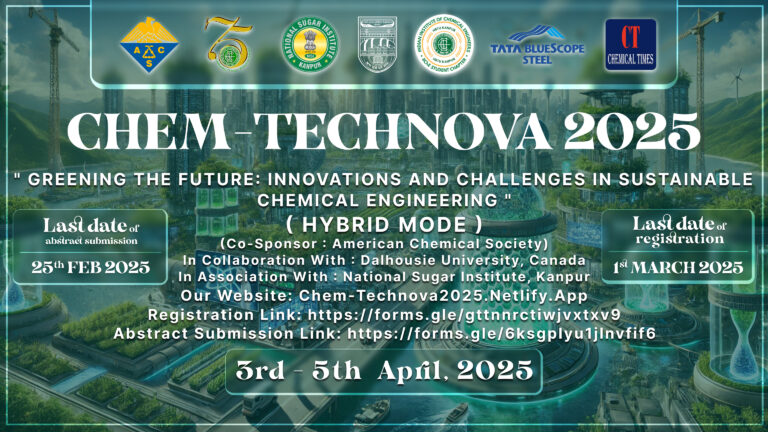