Alloys are mixtures of metals or a metal and a non-metal that are designed to combine the beneficial properties of their constituent elements. One such example is the tin-based alloy, where tin (Sn) serves as the primary metal. Tin, by nature, is a relatively soft and low-strength material, which limits its usefulness in applications that demand higher mechanical strength, durability, and resistance to wear. However, when tin is alloyed with other elements like antimony (Sb), its properties can be significantly improved, making it more suitable for demanding applications.
The addition of antimony to tin-based alloys has been a pivotal development in materials science, offering a range of mechanical, physical, and functional benefits. In this article, we will delve into how antimony improves tin-based alloys, examining the primary benefits such as enhanced hardness, strength, wear resistance, castability, and corrosion resistance. Moreover, we will explore the various industrial and commercial applications where these enhanced alloys are utilized, from bearing materials to solders and coatings.
What is Antimony?
Antimony is a chemical element with the symbol Sb and atomic number 51. It is a metalloid, meaning it has properties that are intermediate between metals and non-metals. In its pure form, antimony is brittle and silvery-white in appearance. Although antimony is not widely abundant in the Earth’s crust, it plays an important role when alloyed with other metals, especially in improving the mechanical properties of tin, lead, and copper.
Antimony is used in various industrial processes, including the manufacturing of batteries, flame retardants, and as an additive in alloys to improve their overall performance. When it comes to tin-based alloys, even small amounts of antimony (usually less than 10%) can drastically alter the physical properties of the alloy, making it significantly more useful in a range of industrial applications.
How Antimony Improves Tin-Based Alloys
When antimony is added to tin, the resulting alloy exhibits several enhanced properties. These improvements are crucial for applications requiring strength, durability, and resistance to wear. Let’s explore how antimony achieves these improvements:
1. Increased Hardness
One of the most significant effects of adding antimony to tin-based alloys is the increase in hardness. Tin, by itself, is relatively soft compared to other metals, and its applications are limited to areas where high hardness is not necessary. However, when antimony is introduced into the alloy, it forms a solid solution with tin that increases the overall hardness of the material.
The addition of antimony disrupts the tin’s crystal structure, resulting in a harder material. This increase in hardness is particularly valuable in applications where the alloy is exposed to mechanical stress or wear, as it allows the material to withstand deformation and resist indentation. For example, in the production of bearings, hard surfaces are necessary to minimize wear and ensure the longevity of the component.
As hardness increases, the material becomes less prone to surface deformation under high pressure, which improves its ability to handle mechanical loads. This is why tin-antimony alloys are used in applications like bearing materials, where high hardness is required to ensure that the material performs well over extended periods of use.
2. Improved Strength
In addition to enhancing hardness, antimony improves the strength of tin-based alloys. Tin itself is a relatively soft metal and lacks the mechanical strength required for many structural applications. However, when alloyed with antimony, tin-based alloys exhibit a marked increase in tensile strength, which is a measure of the material’s ability to withstand pulling forces without breaking.
Antimony contributes to this improvement by strengthening the atomic structure of the alloy. Its presence increases the overall rigidity of the alloy, making it more resistant to deformation under stress. This is particularly useful in applications where the alloy must support weight or endure mechanical stress, such as in engine components, machinery parts, and structural elements.
For instance, in the automotive and industrial sectors, components that undergo high levels of stress, such as engine bearings or bushings, benefit from the enhanced strength provided by tin-antimony alloys. The combination of improved tensile strength and resistance to deformation makes these alloys highly desirable for a wide range of high-performance applications.
3. Enhanced Wear Resistance
One of the most notable improvements that antimony imparts to tin-based alloys is wear resistance. Wear resistance is crucial in applications where the material is subjected to repeated friction or abrasive forces. Tin, in its pure form, is prone to wear and degradation under friction, making it unsuitable for applications where prolonged contact with other surfaces is common.
By adding antimony to tin, the resulting alloy becomes significantly more resistant to wear. Antimony hardens the tin’s surface, making it more durable when exposed to friction. This improvement is particularly valuable in applications like bearings, gears, and piston rings, which must perform reliably over long periods of use while being exposed to constant friction. The wear resistance of these alloys significantly prolongs their service life, reducing maintenance costs and improving the efficiency of the components they are used in.
In industries like automotive engineering, where components such as engine parts and turbochargers are subjected to continuous friction and wear, the enhanced wear resistance of tin-antimony alloys makes them an ideal choice. By reducing the rate of wear, these alloys help improve the longevity and reliability of critical machinery.
4. Improved Castability
Another important advantage of adding antimony to tin-based alloys is the improvement in castability. Castability refers to a material’s ability to flow easily into molds during the casting process and form complex shapes without defects. This is an essential property in industries that rely on the casting of metal components, such as automotive manufacturing and aerospace industries.
Antimony increases the fluidity of tin-based alloys during casting, allowing for smoother mold filling and better-quality castings. This property is particularly useful when manufacturing components with intricate designs or fine details. As a result, the tin-antimony alloy can be easily shaped into various parts such as gear wheels, machine components, and electrical connectors.
The enhanced castability of tin-antimony alloys also reduces the chances of defects like air pockets, shrinkage cavities, or porosity in the final product. This leads to more consistent and reliable products, which is crucial for high-precision applications in manufacturing.
5. Corrosion Resistance
Although antimony does not directly enhance the corrosion resistance of tin, its addition can help improve the overall durability of tin-based alloys in specific environments. For example, in applications where the material is exposed to chemicals or moisture, the increased hardness and strength provided by antimony help reduce the risk of corrosion.
Moreover, antimony can also contribute to the alloy’s ability to withstand oxidative processes, particularly when exposed to high temperatures or aggressive environments. This is useful in applications where the material will be exposed to extreme conditions, such as marine environments, automotive systems, and chemical processing plants.
Applications of Tin-Antimony Alloys
The improved properties of tin-antimony alloys make them ideal for a variety of applications across numerous industries. Below are some key applications where these enhanced alloys are utilized:
1. Bearings and Bushings
Tin-antimony alloys are widely used in the manufacture of bearings and bushings, components that require excellent wear resistance, strength, and low friction properties. These alloys ensure that these parts perform well in machinery, automotive engines, and other heavy-duty applications where reliable movement and reduced friction are necessary.
2. Soldering
Tin-antimony alloys are also used in soldering applications. In the electronics industry, solders are used to join metal components. Antimony, when added to tin-based solders, increases their strength, making them ideal for applications requiring durability and resistance to high temperatures. This is particularly valuable in the production of electronic components, circuit boards, and automotive electronics.
3. Electrical Components
The improved castability and wear resistance of tin-antimony alloys make them suitable for use in electrical connectors, terminals, and other electrical components. The alloys are durable enough to withstand the mechanical stresses encountered in these applications, providing long-lasting performance in electrical systems.
4. Coatings and Protective Materials
Tin-antimony alloys are used in coatings for machinery, electrical components, and automotive parts. These coatings provide a protective layer that reduces wear, corrosion, and friction, enhancing the longevity of the underlying materials. This application is particularly common in automotive parts exposed to harsh environmental conditions.
Conclusion
The addition of antimony to tin-based alloys brings about several significant improvements that make these alloys highly suitable for demanding industrial applications. Antimony enhances the hardness, strength, wear resistance, castability, and overall durability of tin-based alloys, making them indispensable in sectors like automotive engineering, electronics, and machinery manufacturing.
By combining the favorable characteristics of tin with the improvements provided by antimony, these alloys are able to meet the stringent requirements of modern engineering and manufacturing. Whether in bearing materials, soldering, or electrical components, tin-antimony alloys offer exceptional performance that ensures reliability, longevity, and cost-efficiency in a wide range of applications.
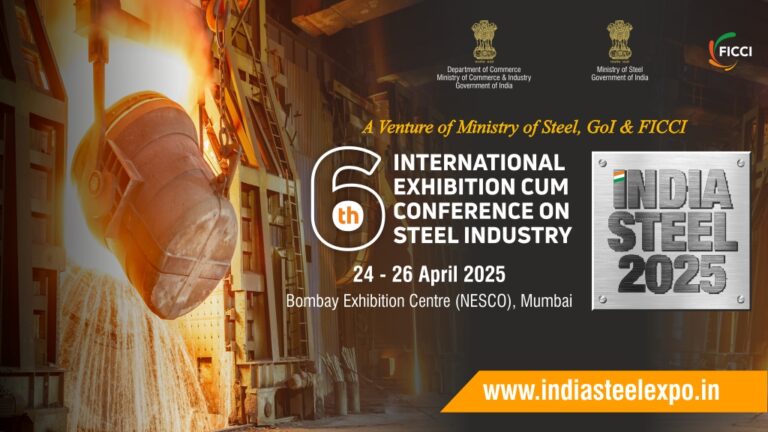