The materials used in the manufacturing of industrial tools and infrastructure components are critical to ensuring their durability, efficiency, and performance. Among the most important and widely used materials are carbon steel and alloy steel, both of which are known for their mechanical properties that make them ideal for applications requiring high impact resistance, wear resistance, and strength. Two key applications where these materials are prominently used are in the construction of hammers and railway rails.
Hammers and railway rails are vital components in a range of industries, and the material choices for these items must meet strict requirements for performance under extreme conditions. This article will explore the materials commonly used for manufacturing hammers and railway rails, focusing on carbon steel and alloy steel. We will also discuss why these materials are selected and how they are processed to enhance their performance in demanding applications.
Hammers: Materials and Manufacturing Considerations
Hammers are essential tools used in a variety of industries, from construction to metalworking, woodworking, and mining. Their primary function is to deliver force to an object, such as driving nails, shaping metal, or breaking apart materials. Given the impact-driven nature of their operation, the materials used for manufacturing hammer heads must be able to withstand repetitive shocks and maintain their integrity over time.
Carbon Steel in Hammer Production
Carbon steel is the most common material used for hammer heads due to its high strength, affordability, and suitability for impact resistance. Carbon steel contains a varying percentage of carbon, typically between 0.05% and 2%, which directly affects its hardness and strength. As carbon content increases, the steel becomes harder but less ductile. For hammers, a balanced carbon content is essential to provide a good combination of strength and toughness, allowing the hammer to absorb shock without cracking or breaking under pressure.
The typical types of carbon steel used in hammer heads are medium-carbon steel and high-carbon steel:
Medium-carbon steel (0.3% to 0.6% carbon content) is commonly used for hammers. It strikes a balance between hardness and toughness, making it suitable for most general-purpose hammers.
High-carbon steel (0.6% to 1.0% carbon content) is often used for hammers designed for heavier-duty applications, such as those used in forging or demolition, where high hardness and wear resistance are crucial.
When using carbon steel for hammers, manufacturers often apply a heat treatment process like quenching and tempering to further enhance the hardness of the hammer’s head. Quenching involves heating the steel to a high temperature and then rapidly cooling it in water or oil, which hardens the material. Tempering is a subsequent heat treatment that reduces brittleness and ensures the hammer remains tough, absorbing shock without shattering or cracking under heavy impact.
Alloy Steel in Hammer Manufacturing
In certain specialized hammer applications, alloy steel is preferred due to its ability to provide enhanced performance in terms of hardness, wear resistance, and toughness. Alloy steels are carbon steels that contain additional alloying elements, such as chromium, molybdenum, vanadium, or nickel. These elements improve the steel’s properties by making it more resistant to wear, corrosion, and fatigue.
Chromium and molybdenum are particularly valuable in alloy steels for hammers because they increase the steel’s resistance to wear and fatigue. These properties are important in tools that are repeatedly struck and subjected to high forces.
Vanadium enhances the steel’s strength and hardness while improving its resistance to shock and deformation, which is critical in applications where the hammer may be exposed to extreme impacts.
Nickel increases toughness and improves the steel’s resistance to cracking at high impact forces.
Alloy steels are typically more expensive than carbon steel, but their superior performance in harsh environments makes them the material of choice for heavy-duty hammers used in industrial applications such as construction, mining, and metalworking.
The Importance of Heat Treatment in Hammer Durability
Whether made from carbon steel or alloy steel, heat treatment is a crucial part of hammer manufacturing. The process ensures that the steel achieves the right balance of hardness, toughness, and wear resistance to withstand the repetitive impacts and high stresses that hammers are subjected to. By selecting the appropriate alloy, controlling the heat treatment process, and ensuring proper tempering, manufacturers can produce hammers that meet the specific requirements of each application.
Railway Rails: Materials and Performance Requirements
Railway rails are critical infrastructure components that support the weight of trains while ensuring a smooth and stable ride. They are subjected to extreme conditions, including high loads, constant friction, and environmental wear. The materials used for manufacturing railway rails must therefore possess a unique set of properties to ensure their longevity, safety, and ability to withstand constant stress and wear.
Carbon Steel in Railway Rail Production
The most commonly used material for manufacturing railway rails is carbon steel, specifically a type known as rail steel. This steel is typically an alloy containing a controlled amount of carbon (usually between 0.6% and 1.0%), along with other alloying elements like manganese.
Manganese is the key alloying element in rail steel. It acts as a deoxidizer, helping to purify the steel by removing impurities. Manganese also increases the hardness and tensile strength of the steel, allowing the rails to handle the heavy loads of trains without deforming. It improves wear resistance, which is critical as the steel must withstand the friction generated by train wheels.
Manganese also imparts resistance to fatigue in rail steel, which helps prevent cracks from developing due to the cyclic loads trains impose on the rails. Over time, these repeated stresses can cause rail fatigue and eventual failure, but manganese helps slow this process down by improving the steel’s ability to absorb and distribute stress.
Alloy Steel for Enhanced Rail Durability
In some cases, alloy steels are used for railway rails, especially when higher performance is required in demanding environments. Alloying elements such as chromium, vanadium, and titanium may be added to improve specific properties like wear resistance, fatigue resistance, and the ability to withstand high stresses.
Chromium improves hardness and wear resistance, which is essential for rails that encounter high-speed trains and abrasive wheel contact.
Vanadium enhances the steel’s strength and resistance to shock, while titanium improves the material’s ability to resist oxidation and corrosion. These properties are beneficial for railway rails that operate in harsh weather conditions or in environments exposed to moisture.
Railways in colder regions, where ice, snow, and moisture can contribute to corrosion, benefit from the inclusion of elements that help combat these environmental factors. Additionally, alloying elements help improve the steel’s ability to withstand fatigue caused by the repeated loading cycles from passing trains.
Heat Treatment of Railway Rails
Just as with hammers, heat treatment plays an essential role in ensuring the proper mechanical properties for railway rails. After the steel has been cast and shaped into the appropriate form, it is often subjected to a process known as tempering, which improves its toughness and resistance to cracking.
In some cases, rails are also quenched to increase hardness, especially in areas that will be subjected to the most wear. Railway rails are often quenched using a controlled cooling process, which hardens the steel surface and helps to prevent the formation of cracks due to high impact or repeated stress.
Conclusion: The Crucial Role of Material Selection
The selection of the appropriate materials for hammers and railway rails is critical to ensuring their performance, durability, and safety. Both components must be able to endure high stresses, repeated impacts, and significant wear over long periods of use. The carbon steel and alloy steel used for these applications provide a robust combination of strength, toughness, hardness, and wear resistance that allows them to withstand the extreme conditions they face.
For hammers, carbon steel is the material of choice for most applications due to its strength, affordability, and ability to withstand impact. Alloy steels, with additional elements like chromium, molybdenum, and vanadium, are used in more demanding applications where increased hardness and wear resistance are necessary.
For railway rails, the durability of the steel is of paramount importance. Carbon steel, particularly with the inclusion of manganese, is ideal for handling the immense forces generated by passing trains. However, alloy steels with additional elements like chromium, vanadium, and titanium offer enhanced performance, particularly in environments exposed to harsh weather conditions or requiring increased wear and fatigue resistance.
In both cases, the careful selection of materials and the application of heat treatment processes are key to ensuring that these components perform reliably over time. Through these advanced material choices, both hammers and railway rails remain integral to their respective industries, performing efficiently under high stress and wear conditions.
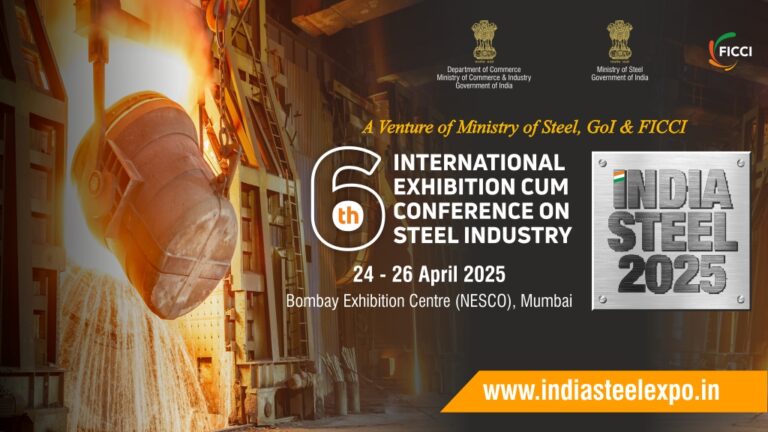