Stainless steel is one of the most versatile materials used across a wide range of industries due to its durability, corrosion resistance, and aesthetic appeal. However, stainless steel is not a single material but a broad category of alloys that are categorized based on their composition and crystalline structure. Among these, certain types of stainless steel exhibit non-magnetic properties, making them highly desirable in various specialized applications.
In this article, we will explore which stainless steels are non-magnetic, why these steels exhibit this property, and where they are used. We’ll also compare non-magnetic stainless steels with other types and explain how the differences in their microstructure impact their magnetic behavior.
What Is Magnetic Behavior in Stainless Steel?
Before diving into which stainless steels are non-magnetic, it’s important to understand why some types of stainless steel are magnetic while others are not. Magnetic behavior in materials is a result of the arrangement of atoms and their associated electron spins. When electrons in a material align in such a way that their magnetic fields reinforce each other, the material becomes magnetic. This is often related to the material’s crystal structure.
Stainless steels come in several different microstructures, including:
Austenitic: This is the most common microstructure of stainless steel and has a face-centered cubic (FCC) crystal structure.
Ferritic: This steel has a body-centered cubic (BCC) crystal structure.
Martensitic: This microstructure has a body-centered tetragonal (BCT) crystal structure.
The magnetic properties of stainless steel are strongly influenced by which of these crystal structures is present in the alloy.
Austenitic Stainless Steel: The Non-Magnetic Champion
Austenitic stainless steels are typically non-magnetic or weakly magnetic, which makes them unique compared to other stainless steel types. The primary reason for this is their FCC (face-centered cubic) crystal structure. In simple terms, the arrangement of atoms in this structure prevents the alignment of magnetic domains, which means that these steels do not exhibit the magnetic properties that other stainless steels with BCC or BCT crystal structures do.
The most common non-magnetic austenitic stainless steels are grades 304 and 316, both of which are widely used across various industries. Let’s take a closer look at these materials:
304 Stainless Steel:
304 stainless steel is the most commonly used type of austenitic stainless steel. It contains 18% chromium and 8% nickel, which gives it its corrosion-resistant properties. The high nickel content stabilizes the austenitic phase of the steel, preventing the formation of magnetic properties. Because of its non-magnetic nature, 304 stainless steel is often used in environments where resistance to rust, corrosion, and staining is needed, without the interference of magnetic fields.
Properties: Non-magnetic, excellent corrosion resistance, good weldability, and formability.
Applications: Food processing equipment, medical instruments, kitchen appliances, and architectural structures.
316 Stainless Steel:
Similar to 304 stainless steel, 316 stainless steel is an austenitic stainless steel but with an additional molybdenum content (about 2-3%). The inclusion of molybdenum significantly enhances its resistance to pitting and crevice corrosion, making it particularly useful in harsh environments such as marine and chemical processing industries.
Properties: Non-magnetic, superior corrosion resistance (especially against chlorides), high strength.
Applications: Marine environments, chemical processing equipment, pharmaceutical manufacturing, and marine hardware.
Both 304 and 316 are non-magnetic under normal conditions. However, they may exhibit weak magnetism if they are subjected to cold working, which can distort the crystal structure slightly and cause some degree of magnetism.
Why Is Austenitic Stainless Steel Non-Magnetic?
The non-magnetic property of austenitic stainless steel is largely attributed to its FCC crystal structure. In this structure, the way the atoms are arranged in a face-centered cubic configuration doesn’t allow for easy alignment of magnetic domains. In contrast to ferritic or martensitic stainless steels, which have a BCC or BCT structure, austenitic stainless steel’s atoms are arranged in such a way that they do not tend to align their magnetic fields in a uniform direction. As a result, the material does not exhibit the magnetic properties that are characteristic of other forms of steel.
Ferritic Stainless Steel: Magnetic in Nature
In contrast to austenitic stainless steels, ferritic stainless steels are magnetic. Ferritic stainless steels have a body-centered cubic (BCC) crystal structure, which allows for the easy alignment of magnetic domains, resulting in magnetic behavior.
Ferritic stainless steels are primarily made with chromium (typically 10.5% to 30%) and very little or no nickel. The absence of nickel stabilizes the ferritic phase, making these steels magnetic. The most common example of ferritic stainless steel is Grade 430, which is often used in applications requiring good corrosion resistance and magnetic properties.
Properties: Magnetic, good corrosion resistance, relatively low cost.
Applications: Automotive exhaust systems, appliances, and industrial applications where magnetic properties are required.
Martensitic Stainless Steel: Also Magnetic
Martensitic stainless steels, like Grade 410 and 420, also exhibit magnetic properties. These steels have a body-centered tetragonal (BCT) crystal structure, which allows for magnetic behavior. Martensitic steels are known for their high strength and hardness, but they typically have lower corrosion resistance compared to austenitic or ferritic stainless steels.
Properties: Magnetic, high strength and hardness, moderate corrosion resistance.
Applications: Cutting tools, blades, valves, and high-stress parts.
Other Factors Affecting the Magnetism of Stainless Steel
While austenitic stainless steels are generally non-magnetic, certain factors can affect their magnetic behavior, such as cold working or welding. Cold working refers to processes like rolling, bending, or stretching, which can cause changes in the crystal structure of austenitic steel and lead to the formation of small amounts of martensite, a magnetic phase. This means that although austenitic stainless steels are usually non-magnetic, they can acquire some magnetic properties when subjected to significant deformation.
Similarly, welding can also cause localized changes in the microstructure of stainless steel, potentially making parts of the material magnetic. For instance, in the heat-affected zone of a welded joint, some austenitic steels may develop martensitic microstructures, leading to weak magnetic behavior.
Applications of Non-Magnetic Stainless Steels
The non-magnetic properties of austenitic stainless steels make them highly useful in applications where the presence of magnetism could interfere with the performance of equipment or machinery. Some common applications include:
1. Medical Equipment and Instruments:
In the medical field, non-magnetic stainless steels like 304 and 316 are crucial in the manufacture of surgical instruments, implants, and medical devices. Magnetism could interfere with sensitive medical equipment such as MRI machines, so the use of non-magnetic materials ensures compatibility.
Examples: Surgical instruments, implants, and MRI-compatible devices.
2. Food Processing:
Non-magnetic stainless steels are used in food processing equipment because they are resistant to corrosion, easy to clean, and do not affect the taste or quality of food. Their non-magnetic properties also make them ideal for use in food packaging machinery and conveyors, where magnetism can disrupt operations.
Examples: Food processing equipment, storage containers, and kitchen appliances.
3. Aerospace:
In the aerospace industry, non-magnetic materials are necessary to avoid interference with sensitive electronic equipment and navigational systems. Non-magnetic stainless steels are widely used in aircraft components where durability, corrosion resistance, and non-interference with magnetic fields are essential.
Examples: Aircraft parts, aircraft engines, and high-performance components.
4. Marine Applications:
Marine environments, especially in saltwater, are harsh and can cause significant corrosion. 316 stainless steel, which is non-magnetic and highly resistant to pitting and crevice corrosion, is often used in marine environments for hardware such as boat fittings, marine shafts, and corrosion-resistant fasteners.
Examples: Marine hardware, corrosion-resistant fasteners, and boat fittings.
Conclusion
The properties of stainless steel are significantly influenced by the crystal structure of the material. Austenitic stainless steels, with their FCC crystal structure, are typically non-magnetic, making them highly suitable for applications where magnetic interference would be detrimental. Grades such as 304 and 316 are the most commonly used non-magnetic stainless steels, owing to their combination of corrosion resistance, strength, and non-magnetic characteristics.
In contrast, ferritic and martensitic stainless steels, with their BCC and BCT crystal structures, are magnetic and are used in applications where magnetism is beneficial or not a concern. Understanding the different types of stainless steel and their magnetic properties is essential for selecting the appropriate material for any given application.
Ultimately, non-magnetic stainless steels have widespread use across a variety of industries, from medical to marine, where their properties help ensure the reliability and efficiency of critical systems and equipment.
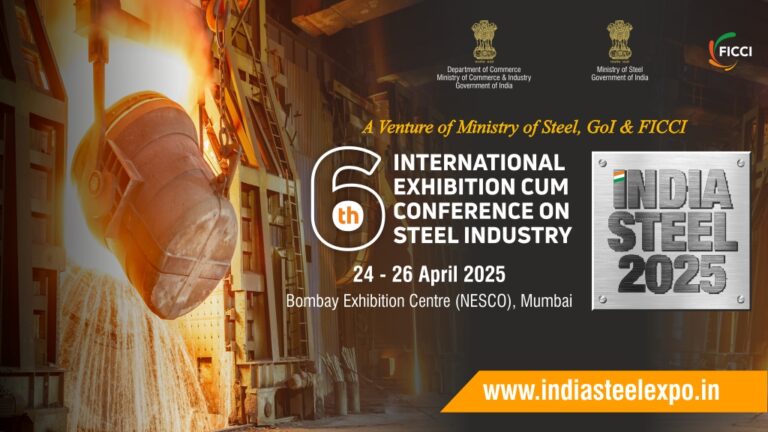