Bearings are integral components in a wide variety of machinery, enabling smooth rotation or movement by reducing friction between moving parts. In particular, heavy-duty bearings are designed to operate under challenging conditions, including high loads, elevated speeds, and harsh environments. These bearings are essential for industries that demand maximum durability and reliability. Whether in mining, automotive, or industrial machinery, heavy-duty bearings must withstand extreme conditions while maintaining high performance. Therefore, selecting the right material for these bearings is crucial, and different materials are chosen depending on the application.
This article explores the various materials used in the manufacturing of heavy-duty bearings, discussing their properties, advantages, and applications.
What Are Heavy Duty Bearings?
Heavy-duty bearings are specialized components designed to carry large loads and resist wear and tear in high-stress environments. Unlike standard bearings, which may be used for lighter or less demanding applications, heavy-duty bearings are engineered to endure the significant forces found in industries like construction, automotive, aerospace, mining, and manufacturing. These bearings must not only handle high radial and axial loads but also maintain precision and reliability even in the most challenging conditions.
The performance of heavy-duty bearings depends heavily on the material used to make them. Factors such as load-bearing capacity, resistance to wear, fatigue strength, and corrosion resistance all play a significant role in ensuring the bearing can withstand its intended use. Understanding these requirements, manufacturers have developed various bearing materials, each designed for specific heavy-duty applications.
Key Materials Used in Heavy-Duty Bearings
1. Chrome Steel (AISI 52100)
One of the most commonly used materials for heavy-duty bearings is chrome steel, also known as AISI 52100. This is a high-carbon steel that contains chromium to improve hardness and wear resistance. Chrome steel bearings are known for their excellent fatigue strength and resistance to wear, making them suitable for high-load and high-speed applications.
Properties: High hardness, excellent wear resistance, good fatigue strength, and dimensional stability.
Advantages: Chrome steel bearings perform well in high-speed applications, offer good resistance to wear, and maintain their shape under stress.
Applications: These bearings are frequently used in automotive components, industrial machinery, and motors due to their combination of strength and durability. Chrome steel bearings are also used in high-performance applications where precision is crucial, such as in spindles and gearboxes.
Chrome steel’s balance of strength, hardness, and cost-effectiveness makes it one of the most popular choices for heavy-duty bearings.
2. Stainless Steel (AISI 440C)
For applications where corrosion resistance is essential, stainless steel bearings made from AISI 440C are often preferred. Stainless steel is a high-chromium alloy that offers both excellent strength and resistance to rust and corrosion. AISI 440C, a high-carbon stainless steel, is particularly suitable for heavy-duty bearings due to its superior mechanical properties.
Properties: High corrosion resistance, high hardness, wear resistance, and good fatigue strength.
Advantages: Stainless steel bearings are ideal for applications in moist, humid, or corrosive environments. They perform well in situations where the bearing may be exposed to chemicals, water, or salt.
Applications: Marine equipment, food processing, and chemical processing industries frequently use stainless steel bearings due to their resistance to corrosion. Additionally, stainless steel bearings are used in medical equipment where cleanliness and corrosion resistance are vital.
The ability of AISI 440C stainless steel bearings to withstand corrosion makes them essential in applications where other materials would deteriorate quickly.
3. Ceramic Materials (Silicon Nitride)
Ceramic bearings, particularly those made from silicon nitride (Si₃N₄), are known for their exceptional performance in extreme conditions. Silicon nitride bearings offer a unique combination of low density, high hardness, and excellent wear resistance. They also have a higher thermal stability compared to metals, which makes them suitable for high-speed applications or environments where temperatures may fluctuate significantly.
Properties: Lightweight, high hardness, excellent wear resistance, and high-temperature tolerance.
Advantages: These bearings perform well in high-speed applications and can operate at much higher temperatures than metal bearings without losing their structural integrity. Silicon nitride bearings also exhibit reduced friction, which improves performance and longevity.
Applications: Aerospace, high-speed machinery, and precision instruments often rely on ceramic bearings. These bearings are especially useful in aircraft engines, turbine generators, and high-performance automotive applications.
Although ceramic bearings are typically more expensive than traditional metal bearings, their performance in high-speed and high-temperature applications often justifies the cost.
4. Carburized Steel
Carburized steel is steel that has been treated to increase its surface hardness through a process called carburizing, where carbon is introduced into the steel at high temperatures. This process results in a hard outer surface, while the core remains tough and ductile. Carburized steel bearings have a high surface hardness, which makes them resistant to wear, while maintaining the ability to absorb shock loads without cracking.
Properties: High surface hardness, excellent wear resistance, and good core toughness.
Advantages: Carburized steel bearings are perfect for applications that experience high-pressure loads and significant wear, as they are able to resist surface damage while maintaining internal toughness.
Applications: Automotive and industrial machinery, especially in gear systems, axles, and high-load applications where durability is a priority, often use carburized steel bearings.
The combination of toughness and wear resistance makes carburized steel an excellent choice for heavy-duty applications involving high shock loads.
5. Bronze and Copper Alloys
Bronze and copper alloys are frequently used in bearings where corrosion resistance and low friction are important. Bronze, especially in the form of tin bronze or phosphor bronze, is known for its ability to operate without lubrication, making it ideal for applications where lubrication is difficult or impossible.
Properties: Good corrosion resistance, self-lubricating properties, good load distribution, and resistance to wear.
Advantages: Bronze and copper alloys can withstand the exposure to moisture, chemicals, and harsh environments. Their self-lubricating properties reduce the need for external lubricants, making them ideal for difficult or remote environments.
Applications: Marine bearings, mining equipment, agricultural machinery, and construction equipment often use bronze or copper alloy bearings due to their resilience in extreme conditions.
Bronze bearings are particularly useful in marine environments where saltwater exposure is common, and in mining or agricultural applications that require continuous operation in rough conditions.
6. Polymer Bearings (e.g., PEEK, PTFE)
In some heavy-duty bearing applications, polymers like PEEK (Polyetheretherketone) and PTFE (Polytetrafluoroethylene) are used. These materials offer lightweight alternatives to metal and ceramic bearings, and they provide excellent chemical resistance, low friction, and self-lubricating properties.
Properties: Lightweight, corrosion-resistant, self-lubricating, and able to operate in high-temperature environments.
Advantages: Polymer bearings are ideal for situations where metals might fail due to corrosion or friction. Their self-lubricating properties allow for smoother performance with less maintenance.
Applications: Aerospace, chemical processing, and machinery that operates in harsh environments often use polymer bearings. For example, PEEK bearings are used in high-temperature and high-performance settings like automotive engines or aerospace applications.
Although polymer bearings typically can’t carry as much load as their metal counterparts, their lightweight nature and ability to resist chemical exposure make them valuable in specific industries.
7. Tungsten Carbide
Tungsten carbide is a hard, dense material that is known for its extreme hardness and excellent wear resistance. Tungsten carbide bearings are ideal for industries that involve heavy abrasive conditions or high pressures.
Properties: Extreme hardness, excellent wear resistance, and high durability in abrasive environments.
Advantages: Tungsten carbide bearings are able to withstand the stresses of industries that deal with harsh conditions and abrasive materials. They are often used in applications where wear resistance is more important than weight or cost.
Applications: Mining, drilling, and rock crushing industries benefit from tungsten carbide bearings, as these bearings can survive the extreme conditions found in these industries without degrading.
Tungsten carbide bearings are less common but are invaluable in environments where high hardness and wear resistance are required, such as in mining or construction.
Conclusion
Heavy-duty bearings are critical to the performance and longevity of machinery that operates under extreme conditions. The materials used to manufacture these bearings — such as chrome steel, stainless steel, ceramic materials, carburized steel, bronze, polymers, and tungsten carbide — are selected based on specific needs such as load capacity, speed, corrosion resistance, temperature tolerance, and wear resistance.
Understanding the advantages and limitations of each material ensures that engineers can choose the most appropriate bearings for their applications. For industries like automotive, mining, aerospace, marine, and industrial machinery, the selection of heavy-duty bearings is vital to ensuring reliability, efficiency, and longevity.
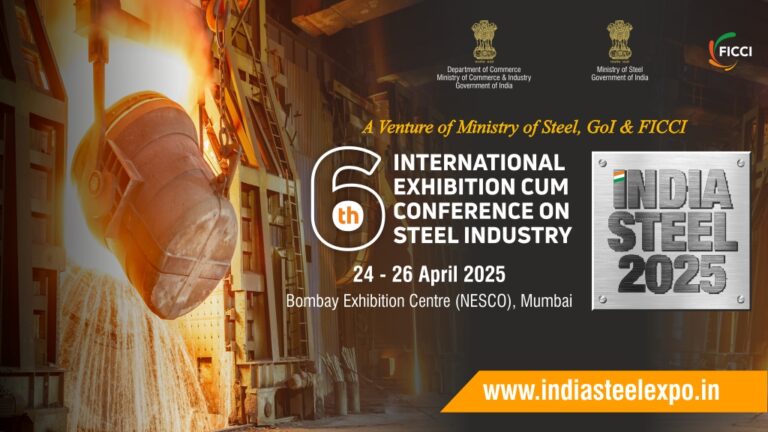