Aluminium is one of the most versatile materials used in modern construction and manufacturing. Known for its light weight, excellent corrosion resistance, and versatility, aluminium has been used across a range of industries, including construction, aerospace, automotive, and packaging. However, despite these advantages, aluminium does have its drawbacks, especially when compared to other materials like steel or concrete.
Although aluminium is often viewed as a top choice due to its desirable qualities, it suffers from a range of disadvantages that need to be carefully considered when determining its suitability for construction purposes. Some of the most significant disadvantages of aluminium as a material of construction include its lower strength compared to steel, higher cost, limited performance at high temperatures, and susceptibility to corrosion in certain environments. These limitations, combined with challenges in fabrication, impact its effectiveness in specific applications.
In this article, we explore the various disadvantages of aluminium, highlighting the challenges and limitations that may affect its use in construction projects.
1. Lower Strength Compared to Steel
One of the most significant drawbacks of aluminium as a construction material is its lower strength relative to steel. While aluminium is lightweight, it is not as strong as many other materials, particularly steel, which is often the material of choice for load-bearing structures and high-stress applications. The strength-to-weight ratio of aluminium, though impressive, falls short of the capabilities of steel in many instances.
Aluminium is softer and more malleable than steel, meaning it may not be the best material choice when a project demands significant structural integrity or the ability to withstand heavy loads over time. Steel, particularly high-strength alloy steels, offers much greater tensile strength, compressive strength, and impact resistance, making it the preferred choice in applications that involve heavy-duty construction, high-rise buildings, and bridges.
Applications Requiring Strength: For buildings and bridges that are subjected to substantial loads, such as high winds, heavy traffic, or the weight of the structure itself, aluminium may not offer the load-bearing capacity that steel can provide. Steel’s superior strength-to-weight ratio makes it more appropriate for these applications.
Alloying Aluminium for Strength: While aluminium can be alloyed with other metals, such as copper, magnesium, and zinc, to improve its strength, even the strongest aluminium alloys still fail to match the strength of steel, particularly when dealing with large, industrial-scale constructions.
2. Cost and Economic Considerations
Aluminium is typically more expensive than materials like steel or concrete, particularly when factoring in the cost of production and energy usage involved in aluminium extraction. The production process for aluminium is highly energy-intensive, requiring large amounts of electricity for the electrolytic reduction process used to extract aluminium from bauxite ore. As a result, the production cost of aluminium tends to be significantly higher than many other materials, making it a more expensive option for large construction projects.
Energy-Intensive Production: Extracting and refining aluminium is an energy-demanding process, which makes aluminium products more costly than other construction materials like steel, which generally has a more established and energy-efficient production process.
Price Fluctuations: The cost of aluminium can fluctuate significantly based on global energy prices and the demand for aluminium in various industries, including construction, aerospace, and electronics. For projects with a tight budget, the high cost of aluminium can become a major limitation.
Although aluminium can offer some savings due to its light weight (resulting in reduced transportation costs), the initial investment cost of using aluminium as a material may still make it an impractical choice for budget-conscious projects, especially when alternatives like steel or concrete offer similar structural benefits at a lower cost.
3. Limited Performance at High Temperatures
Aluminium’s performance at high temperatures is one of its most significant limitations in certain construction and industrial applications. Unlike steel, which can withstand very high temperatures, aluminium tends to weaken as temperatures rise, leading to a reduction in its strength and durability. This makes aluminium unsuitable for high-temperature environments where heat resistance is a key factor in material selection.
Melting Point: The melting point of aluminium is approximately 660°C (1220°F), which is much lower than that of steel (1370°C or 2500°F), limiting its ability to function in environments where materials need to maintain their integrity at elevated temperatures.
Thermal Expansion: Aluminium expands and contracts more than steel when exposed to temperature changes, which can result in issues with dimensional stability in environments where temperature fluctuations are common. This can be problematic in construction applications where maintaining exact dimensions is important, especially for structural elements that must fit together precisely.
Fire Safety: In fire-prone environments, aluminium’s inability to maintain strength at high temperatures can result in structural failure or degradation. Steel, on the other hand, retains much of its strength even in high-heat situations, making it the preferred material for fire-resistant structures.
For construction projects in areas prone to extreme heat or fire hazards, the reduced performance of aluminium at high temperatures is a major disadvantage. In such cases, fireproofing or the use of more heat-resistant materials may be necessary.
4. Corrosion in Certain Environments
Although aluminium is naturally corrosion-resistant due to the formation of a protective oxide layer on its surface, it is still susceptible to certain types of corrosion under specific environmental conditions. This is particularly true when aluminium is exposed to moisture, salts, or other aggressive chemicals, which can compromise its protective oxide layer and lead to corrosion or material degradation.
Galvanic Corrosion: When aluminium comes into contact with more noble metals (such as copper, stainless steel, or brass), particularly in the presence of moisture, it can undergo galvanic corrosion. This occurs because of the difference in the electrochemical potentials between the metals, causing the aluminium to corrode more rapidly.
Chloride-Induced Corrosion: Aluminium is also vulnerable to pitting corrosion when exposed to environments with high levels of chlorides, such as marine environments or areas where road salt is used during winter. In coastal regions or areas with high humidity, aluminium structures can suffer from pitting, which damages the material’s surface and reduces its durability.
Alkaline Corrosion: In highly alkaline environments, such as those with sodium hydroxide (caustic soda), aluminium can corrode more quickly, making it unsuitable for certain chemical processing applications or industrial environments where such conditions are common.
For projects near coastal areas, chemical plants, or other aggressive environments, the potential for corrosion can make aluminium a less attractive option. In these cases, materials like stainless steel or specialty alloys may be a better choice for long-term durability.
5. Susceptibility to Fatigue and Impact Damage
Aluminium, while strong in terms of weight-to-strength ratio, is more susceptible to fatigue and impact damage than other materials, particularly under repeated stress. While it is useful in certain applications due to its ability to absorb vibrations, aluminium’s performance may degrade more rapidly than steel under repeated cycles of loading and unloading.
Fatigue Resistance: Aluminium is more prone to fatigue cracking when subjected to cyclic stresses, especially in dynamic load-bearing applications like automobiles, aircraft, and machinery. Over time, aluminium components can experience cracks and fractures that compromise their structural integrity.
Impact Resistance: Aluminium is also more likely to suffer dents and deformation when subjected to sudden or severe impacts. Steel, by contrast, has a much higher impact resistance, making it a better choice in environments where sudden force or mechanical impacts are common.
This susceptibility to fatigue and impact makes aluminium unsuitable for certain heavy-duty construction applications, where resistance to wear and sudden forces is paramount.
6. Difficulties in Welding and Joining
Aluminium can be more difficult to weld than other metals, especially when it comes to achieving strong, durable joints. The material’s thermal conductivity and its low melting point make it challenging to control the welding process, particularly in high-quality applications.
Welding Complexity: Welding aluminium requires more specialized equipment and expertise compared to steel. Additionally, aluminium oxide, which forms on the surface of the material, must be removed before welding, requiring additional preparation and labor.
Specialized Welding Techniques: Techniques such as TIG welding (tungsten inert gas) or MIG welding (metal inert gas) are often needed to successfully weld aluminium, and these techniques may be more time-consuming and expensive than welding steel.
For large-scale projects that require extensive welding or fabrication, the increased difficulty in welding aluminium can add to both the cost and complexity of the project.
Conclusion
Aluminium is a highly versatile material with many advantages in construction, including light weight, corrosion resistance, and thermal conductivity. However, it does have several significant disadvantages, including lower strength compared to steel, higher production costs, limited high-temperature performance, susceptibility to corrosion, and difficulties in welding. These limitations make aluminium less suitable for certain applications, particularly in environments where strength, durability, or resistance to extreme conditions is crucial.
For construction projects that involve heavy load-bearing, high-stress environments, or exposure to harsh chemicals and high temperatures, other materials, such as steel, concrete, or stainless steel, may be a more appropriate choice. Nonetheless, aluminium’s unique properties make it an excellent material for many construction applications, especially when weight, corrosion resistance, and thermal conductivity are prioritized.
In summary, the decision to use aluminium as a construction material should be carefully considered based on the specific needs of the project, the environmental conditions, and the performance requirements. By understanding its limitations, engineers and architects can make informed choices and select the best materials for each unique application.
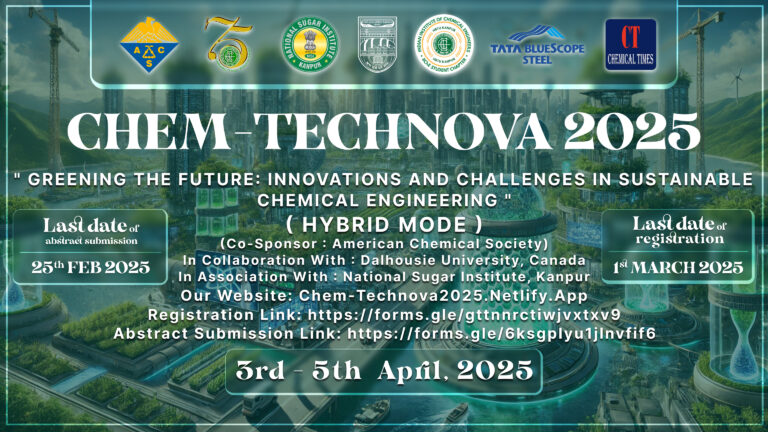